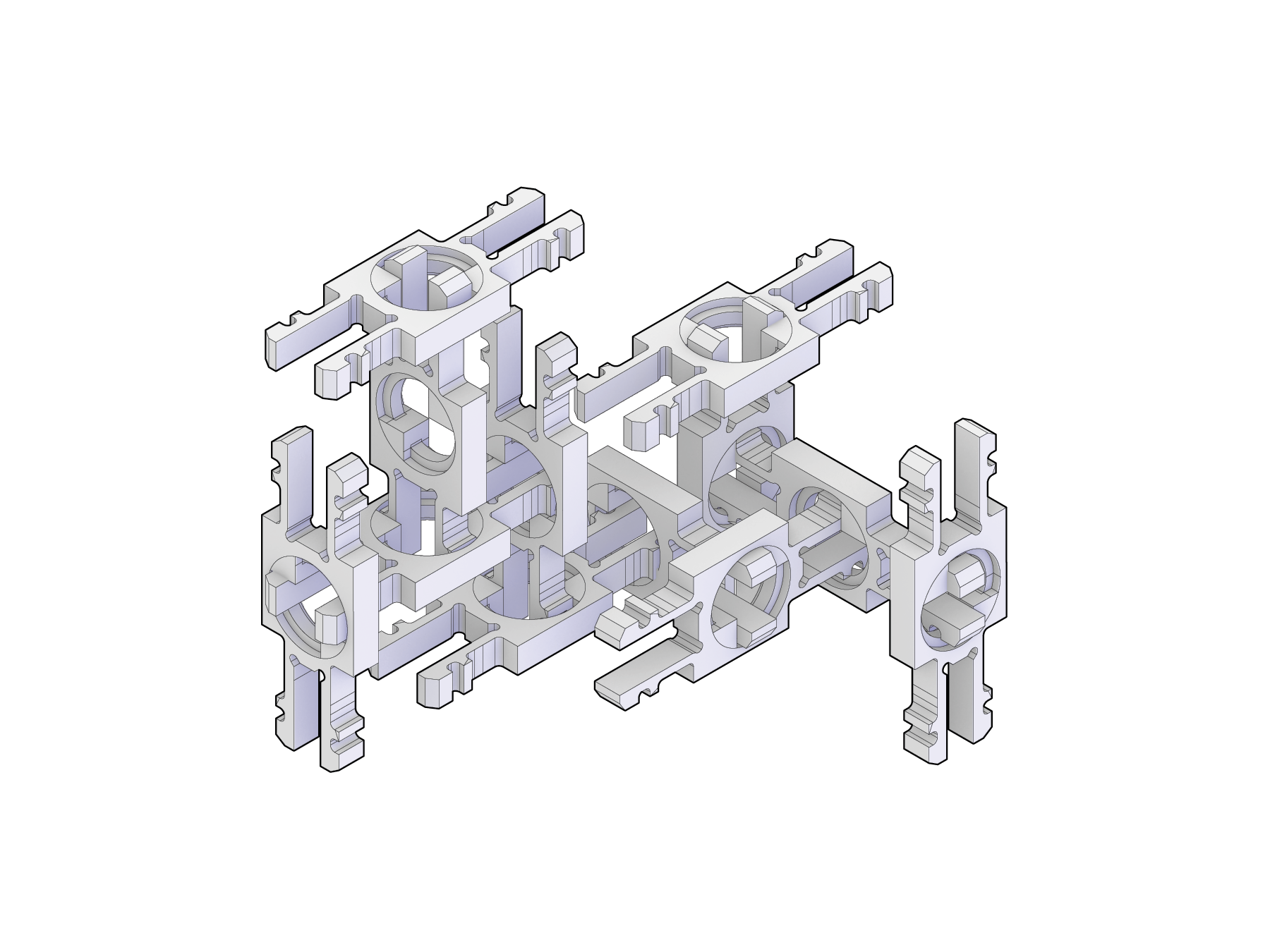
robotic_assemblies
Parametric Joinery Assembly
in partnership with Julia BEitel and kobe phillips
6-axis milling
In the course “Rethinking Timber Joinery: Robotic Fabrication & Design” students were encouraged to take precedents from natural sources and methods of joinery to create systems that allowed for assembly.
With the help of a 6-axis robotic arm, and parametric models, joints were created to interlock and assemble in a larger system of modules.
The end result was a large scale kit of parts that was carved out from 2”x4” pieces of wood that can be recreated in a larger environment.
v1
A1 Joint: Closed-Loop System with Curved Teeth Connections
The A1 joint investigated the integration of traditional and nontraditional timber joinery. Initial inspirations included finger joints, honeycomb structures, and mollusk shells. These elements were synthesized into a closed-loop system that utilized curved male and female teeth to create interlocking connections within
v2
The final iteration, the A3 joint, combined a curved rotational axis plane with a dynamic snapping tooth to connect modular units. This “snapping joint” was designed to flex under pressure and adjust into position by compressing the teeth. Once in place, the joint could rotate along an engraved surface, providing a blend of flexibility and stability.
Fabrication of the A3 joint required advanced milling techniques, including bilateral machining of the timber stock. Milling speed was carefully reduced to minimize vibrations, while the material properties of the teeth—such as length and bandwidth—were calibrated for optimal performance.
fabrication process